Batch Manufacturing
Efficiency, cost, and overall productivity are impacted by a variety of challenges batch manufacturing processes are facing, such as increasing regulatory constraints, including environmental, shortened production batches, accelerated time-to-market and shrinking product lifecycles.
Batch Manufacturing
Batch production is a manufacturing process where a group of identical products is produced at the same time constituting a batch. The batch goes through separate production steps as a whole. Each batch is characterized by attributes with values specific to the batch, These attributes relate back to for example raw materials consumed, equipment used, manufacturing conditions, … Pharmaceutical products, or consumer packaged goods are typical examples of batch manufacturing.
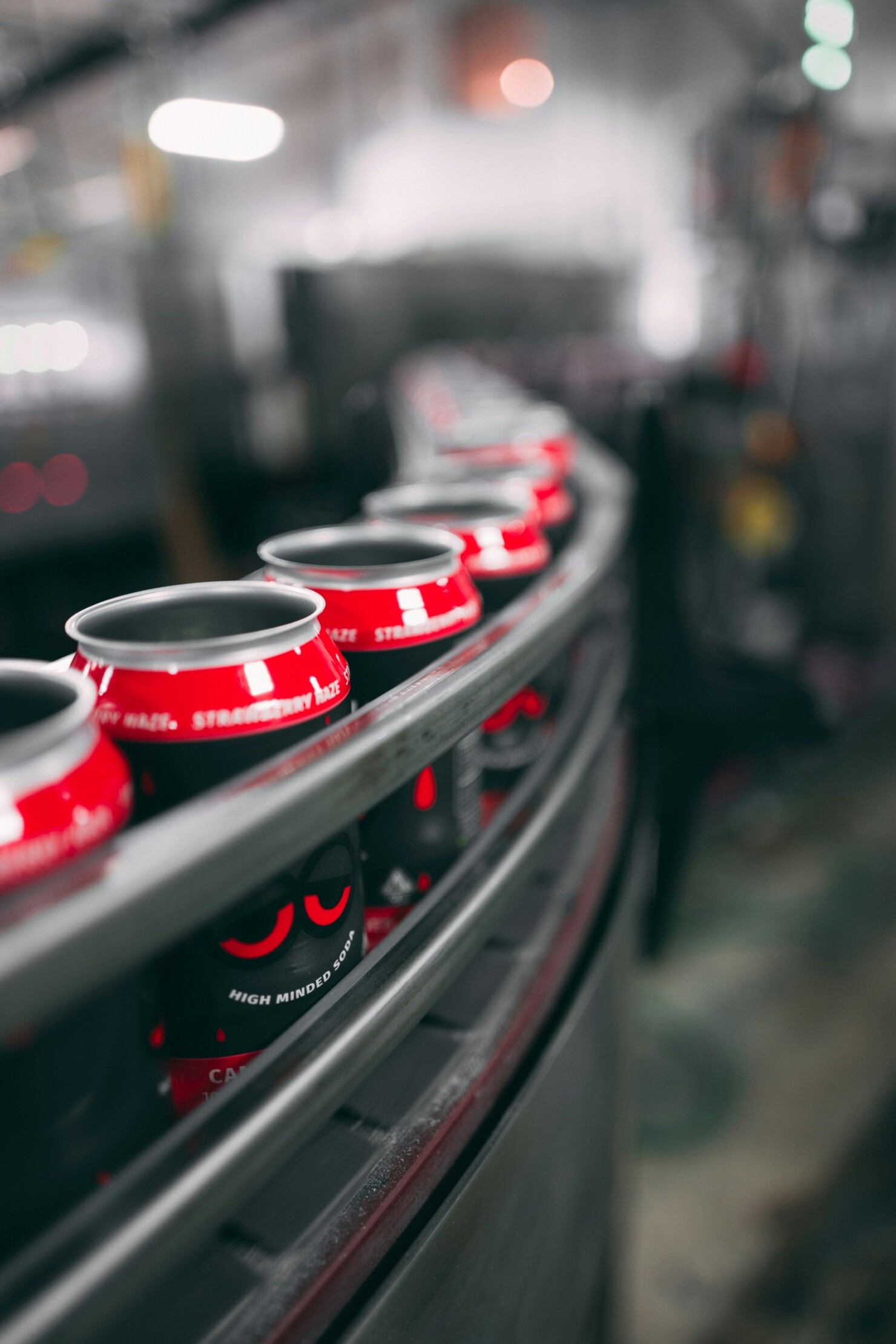
In batch manufacturing, changeovers between batches imply production downtime and may result into reduced efficiency due to frequent production lines setup and preparation in between batches.
-
Increasing regulatory constraints, including environmental
Regulatory compliance is a critical aspect of batch manufacturing, with increasing constraints:
- Stringent Regulations: manufacturers must adhere to rigorous standards to ensure product safety, quality, and environmental sustainability. This includes compliance with Good Manufacturing Practices (GMP), environmental regulations, and industry-specific standards. It often implies that the extended supply chain planning and execution process related to a product shall undergo a qualification process.
- Environmental Impact: there is growing pressure to minimize the environmental footprint of manufacturing processes. This includes reducing emissions, waste, and energy consumption. Compliance with environmental regulations often requires on the one hand significant investment in new technologies and processes and on the other hand deployment of continuous improvement approaches.
- Documentation and Traceability: Maintaining detailed records and ensuring traceability of materials and processes are essential for compliance. This can be resource-intensive and requires robust systems for data management, consolidation and reporting.
- Continuous Monitoring and Validation: Regular monitoring and validation of processes are necessary to ensure ongoing compliance. This involves implementing qualification processes and quality control measures as well as conducting regular audits.
-
Shortened production batches
The trend towards shortened production batches presents several challenges for batch manufacturers:
- Flexibility and Adaptability: Shorter production batches require manufacturers to be more flexible and adaptable in their operations. This involves frequent changeovers and adjustments to production lines, which is time and resources-consuming. When ill planned and organized, changeovers can direly impact production lines efficiency.
- Inventory Management: Managing inventory effectively becomes more complex with shorter batches. Manufacturers need to balance the need for sufficient raw materials and components with the risk of overstocking. The pharmaceutical or consumer packaged goods manufacturers often operate in a context of constrained products shelf life and / or storage conditions which add complexity to inventory management across the extended supply chain.
- Quality Control: Ensuring consistent quality across multiple short batches can be challenging. Each batch may be subject to intensive quality checks, which can slow down production and increase costs.
- Cost Implications: Shorter batches can lead to higher per-unit production costs due to increased setup times and reduced economies of scale.
-
Accelerated Time-to-Market
In batch manufacturing the need for accelerated time-to-market is for instance triggered by promotions deployment, packaging changes and / or pharmaceutical form evolution. Time-to-market faces significant difficulties:
- Speed and Efficiency: Manufacturers must streamline their processes to reduce lead times and bring products to market faster. This involves optimizing extended supply chain workflows and reducing bottlenecks while leveraging advanced technologies.
- Innovation and Development: Rapid product development is essential to stay competitive. This requires efficient design, prototyping and qualification processes, as well as the ability to quickly scale up the extended supply chain, including means of production. Transition from product development to industrialization is key.
- Regulatory Approval: Accelerating time-to-market must be balanced with the need to obtain regulatory approvals, which can be time-consuming. Manufacturers need to ensure that their products meet all regulatory requirements without compromising on speed. Seamless collaboration in-between product development, industrialization department and compliance teams is critical.
- Supply Chain Coordination: Effective coordination with suppliers and logistics partners is crucial to ensure timely delivery of raw materials and components. Any delays in the supply chain can impact the overall time-to-market.
-
Shrinking product lifecycles
Shrinking product lifecycles pose several challenges for batch manufacturers:
- Frequent Product Launches: With shorter product lifecycles, manufacturers need to launch new products more frequently. This requires efficient product development and manufacturing processes to keep up with market demands.
- Demand Forecasting: Accurate demand forecasting becomes more critical as product lifecycles shrink. Manufacturers need to predict market trends and consumer preferences to avoid overproduction or inversely stockouts.
- Inventory Turnover: Managing inventory turnover is challenging with shorter lifecycles. Manufacturers need to ensure that products move quickly through the supply chain to avoid obsolescence. Failing to perform impacts product margins and can lead to significant scrap.
- Sustainability: Shorter lifecycles can lead to increased waste and environmental impact. Manufacturers need to adopt sustainable practices to minimize the environmental footprint of their products.
How we can help
-
Value analysis and Value engineering
-
Supply Chain planning and governance optimization
-
Supplier sourcing and management enhancement
-
Lean manufacturing
-
Supply Chain execution effectiveness
-
Client service and engagement alignment
-
After sales and maintenance operations improvement