Continuous Process Manufacturing
By adopting advanced technologies, improving supply chain management, and focusing on sustainability, continuous process manufacturing must enhance operational efficiency and resilience to cope with health and security risks, raw material availability and price volatility, Work In Progress visibility challenges, and rising environmental pressures.
Continuous Process Manufacturing
Production lines in continuous process manufacturing operate without stops or interruptions 24⁄7. In continuous manufacturing, raw materials are transformed into finished products through a series of interconnected and automated processes. Raw materials are continuously fed into the production system to undergo initial processing steps such as mixing, heating, or chemical reactions. The processed materials move through various stages where they are further refined to be then subjected to final transformation steps.
For example, refinery plants, steel mills or power plants are operated in a continuous manner.
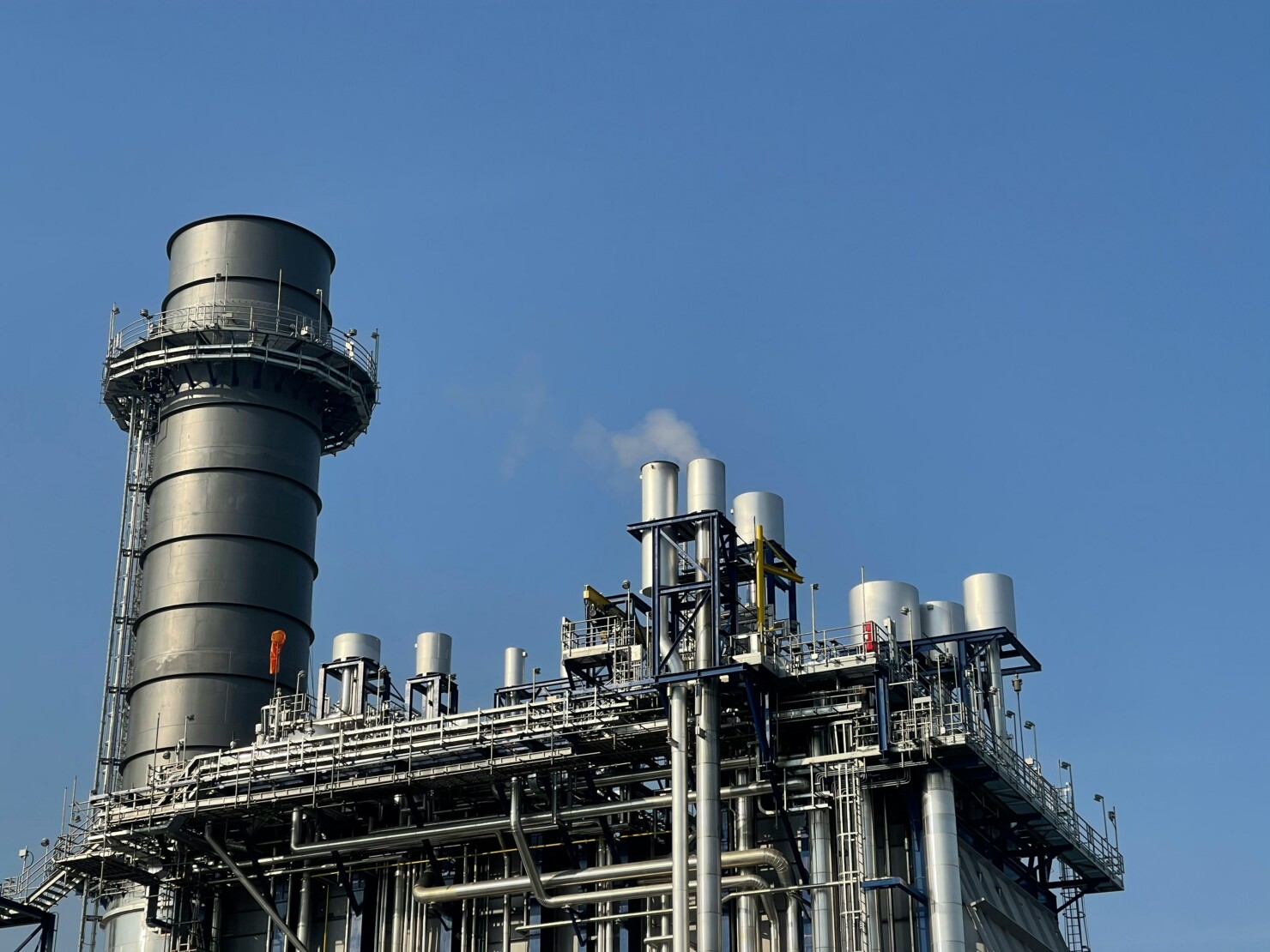
Unintentional pause in the manufacturing process causes product loss and implies complex production restart procedures, resulting into major operational and financial impacts. Plant shutdowns must be carefully planned, turnarounds have generally unique project management characteristics encompassing numerous inspection, testing and maintenance / enhancement operations.
-
Health & Security sensitivity
Health and Security are paramount in continuous process manufacturing due to the potential risks to workers, facilities and the environment. Key challenges include:
- Physical Hazards: Continuous process manufacturing plants are full of automated systems and machines exposing staff to risks such as impact, collision, or being caught between moving parts. Moreover, materials handled are often hazardous and are subject to specific procedures (administrative papers, placarding and marking, loading / unloading, blocking and bracing, incident reporting, …). Continuous process manufacturers ensure that security plans are deployed and complied with.
- Unauthorized Access and Intrusions: Manufacturing facilities are vulnerable to unauthorized access, which can lead to theft, vandalism, or sabotage.
- Cybersecurity Threats: With the rise of Industry 4.0, interconnected systems are more susceptible to cyber-attacks, which can disrupt operations and compromise plant integrity, security and sensitive data.
-
Raw material availability dependency and price volatility
The dependency on raw material availability and prices volatility is a critical challenge for continuous process manufacturing:
- Supply Chain disruptions: Events like trade wars, sanctions, and natural disasters can disrupt supply chains, affecting the availability of raw materials. Manufacturers secure safety stocks and alternative source supply for critical materials when relevant.
- Price volatility: Raw material prices can fluctuate due to global economic trends, geopolitical tensions, natural events, … This volatility impacts product costing and profit margins.
-
Keen on Work-in-process visibility
Work-in-process (WIP) visibility is crucial for maintaining efficiency and profitability in continuous process manufacturing:
- High WIP levels: Excessive WIP ties up valuable capital, increases storage costs, and reduces flexibility. It can also lead to quality issues and increased risk of obsolescence.
- Poor scheduling and bottlenecks management: poor scheduling can foster process inefficiency, especially when bottlenecks are not properly addressed in planning. This can cause high WIP levels, impacting overall production efficiency.
- Lack of real-time visibility: Without real-time visibility into production operations, it is challenging to manage WIP effectively.
Industrial Internet of Things (IIoT) is deployed in continuous process manufacturing to enable real-time monitoring of equipment and of production parameters. This ensures that any potential equipment failures are detected and coped with, any deviations from quality standards are detected and corrected immediately, or any real-time adjustments and optimizations to the manufacturing process are performed.
-
Rising environmental pressure
Environmental concerns are increasingly influencing continuous process manufacturing:
- Sustainability: There is growing pressure to minimize environmental impact by reducing waste, energy consumption, and resource utilization.
- Regulatory compliance: Manufacturers must comply with stringent environmental regulations, which can be costly and complex.
- Public and market Pressure: Consumers and stakeholders are demanding more sustainable practices, pushing manufacturers to adopt greener technologies and processes.
How we can help
-
Value analysis and Value engineering
-
Supply Chain planning and governance optimization
-
Supplier sourcing and management enhancement
-
Lean manufacturing
-
Supply Chain execution effectiveness
-
Client service and engagement alignment
-
After sales and maintenance operations improvement